In modern industrial production, the purity of raw materials often directly determines the quality of the final product. Whether in grain processing, plastics production, or resource recycling, efficiently removing ferromagnetic impurities from raw materials has always been a critical issue. As a highly efficient magnetic separation device, the GRID MAGNET SEPARATOR is becoming an "industrial guardian" on production lines across various industries.
First, what is a barrier magnetic separator?
A barrier magnetic separator is a grid-like magnetic separation device constructed using high-strength permanent magnets or an electromagnetic system. Its primary function is to automatically and continuously remove ferromagnetic impurities from free-flowing powders, granules, or slurries, thereby protecting downstream equipment, ensuring product purity, and improving production safety.
Compared to traditional magnetic separation equipment, the barrier magnetic separator utilizes a unique grid design, providing a larger adsorption area and more efficient processing capacity, making it particularly suitable for handling materials with large flow rates.
Secondly, the core operating principle of a magnetic separator is the precise application of magnetic force. The working principle of a fence magnetic separator is based on the different physical properties of ferromagnetic and non-magnetic materials in a magnetic field:
1. Material Passage: The material to be processed passes through a grid-like array of magnetic bars.
2. Adsorption Separation: Ferromagnetic impurities are captured by the high-intensity magnetic field and adsorbed on the surface of the magnetic bars.
3. Pure Material Passage: After impurities are removed, the pure material continues to the next process.
4. Periodic Cleaning: Adsorbed impurities are periodically cleaned manually or automatically.
This design ensures continuous and efficient production, allowing for uninterrupted operation without downtime.
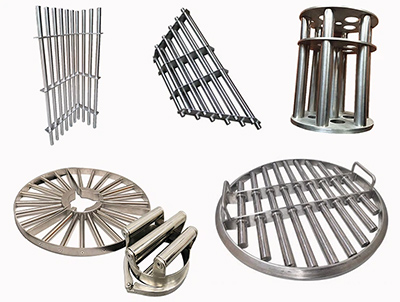
Features:
High-power, low-cost magnetic plates for separating feed materials in hoppers.
Made with strontium ferrite or rare earth neodymium iron boron magnets.
Round or rectangular, with a stainless steel body.
Single or dual element options for optimal separation.
High-temperature resistant grid made of alnico magnets.
Magnets are easily removable for cleaning.
A variety of magnetic screen types are available, including:
Product Purity: Ensures removal of ferrous contaminants, improving product quality
Equipment Protection: Protects processing equipment from damage caused by metal contamination, reducing downtime and repair costs
Compliance: Helps meet audit requirements and industry standards for product safety
Easy Installation and Maintenance: Simple installation, typically requiring no power or maintenance
Versatility: Customizable to various sizes and application requirements
Standard Magnetic Screens: Designed for general applications, available in a variety of sizes and magnetic field strengths
Easy Clean Magnetic Screens: Designed to simplify removal of captured contaminants
Encapsulated Easy Clean Grid Magnetic Separators: Designed as a drop-in replacement for standard vibrating screens
Automatic Magnetic Screens: Self-cleaning grids designed for continuous operation
Industry application scenarios
Food Processing Industry
In the processing of grain, flour, starch, and other foods, fence magnetic separators effectively remove metal impurities from raw materials, ensuring food safety and compliance with HACCP and FDA standards.
Plastics and Chemical Industry
Protecting expensive equipment such as injection molding machines and extruders from damage by metal impurities while improving product quality.
Pharmaceutical Manufacturing
Ensuring the purity of raw materials during the processing of pharmaceutical raw materials and complying with GMP standards.
Recycling Industry
Effectively separating metal impurities during the recycling of waste plastics and waste paper improves the quality of recycled materials.
Mining and Building Materials Industry
Protecting crushing and grinding equipment during ore crushing and cement production, reducing wear and tear.
Please refer to the Installation and Maintenance Guide.
Key Points for Correct Installation
1. Ensure installation in an area with smooth material flow.
2. Maintain a proper installation angle.
3. Allow ample space for cleaning and maintenance.
4. Ensure proper grounding (electromagnetic type).
Daily Maintenance Recommendations
1. Regularly check magnetic strength (every 6 months).
2. Promptly remove adsorbed metal impurities.
3. Inspect seals and for wear.
4. Keep the equipment clean and dry.